齿轮精加工方法(一)
剃齿加工
剃齿加工是软齿面齿轮在滚齿(或插齿)加工后,为提高齿形精度和降低齿面粗糙度常用的一种展成精加工方法。刀具分齿条式剃刀和圆形剃刀。剃刀实质上是一个高精度、具有切削能力的斜齿轮,它和齿坯的机床啮合相当于交错轴斜齿轮的啮合,利用共轭齿面间的相对运动速度,产生切削运动,形成展成切削。
剃齿加工所需运动有:剃齿刀的旋转运动;工件沿轴向的往复运动;工件每往复一次的径向进给运动,见图11-4。
剃齿法的优点是:剃齿机结构简单,调整方便;剃齿加工精度主要取决于刀具精度,能校正部分滚、插加工后齿轮的误差,一般可得到精度6~7级,齿面粗糙度Ra0.8~0.2μm的齿轮;生产率高,加工一个齿轮仅需2~4min,适合成批生产;加工范围大,对直径6~300mm的内齿轮和直径6~1200mm的外齿轮均可加工。但是剃齿也存在一定的缺点,如不能修正齿轮的公法线长度变动量,剃刀制造困难、不便于加工多联齿轮等。
剃齿加工分轴向剃齿法、对角线剃齿法和切向剃齿法等。
普通剃齿法
是工作台走刀方向和齿坯轴线一致的剃齿加工方法(亦称纵剃法),如图11-5所示。在齿坯的各个端截面都要通过节点P,即由P1移到P2,工作台最小行程Ls应等于齿轮宽度BI。
该方法的优点是:工艺简单,使用较普遍。缺点是:刀具磨损不均匀(剃刀工作部分仅是A-A截面一圈);工作台行程较长,生产率低,使这种剃齿法应用受到限制。
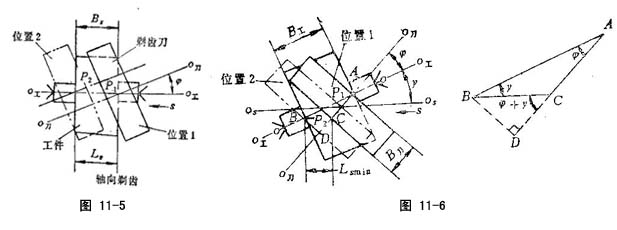
对角剃齿法
是工作台走刀方向和齿坯轴线方向呈γ角(通常γ角=15°~35°)的剃齿方法,如图11-6所示。剃齿时,随着工作台的移动,剃齿刀和齿轮节点位置发生变化,使剃齿刀在整个齿宽上磨损均匀,可提高刀具耐用度,增大径向进给量。
该方法,工作台的行程可随γ角增大而减小,比普通剃齿法短。和普通剃齿法相比,生产率可提高3~4倍,刀具耐用度可提高约1倍。但要求剃齿机床工作台必须可调角度,并且机床有较高的刚度和较大的功率。此外,还要求节点P1、P2的变化范围在剃齿刀有效工作长度之内,调整的工艺水平要求高。
节向剃齿法(横剃法)
当工作台走刀方向和被加工齿轮的轴线方向夹角γ增大到90°时,对角剃齿就成了切向剃齿,如图11-7所示。这时工作台行程与其他剃齿法相比更短,生产率更高。切向剃齿时,剃齿刀宽度和工作行程长度的计算式为:b0=b/cosφ,Lsmin=b.tgφ。
该方法具备了对角剃齿法的优点。其生产率比对角剃齿法还高。
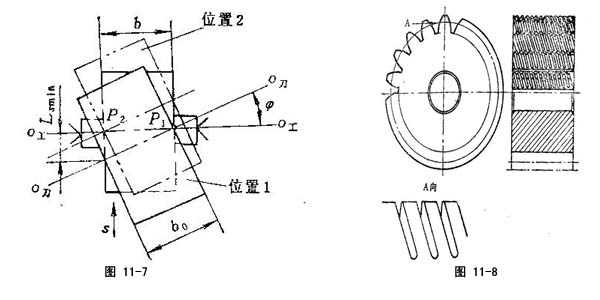
过盈啮合剃齿法
在工件与刀具的齿面上采用加压的方式,使刀具和齿坯无侧隙啮合,从而缩短中心距,进行剃齿的方法。
此法的优点是:剃齿机的结构简单,应用较广。一般所说剃齿就是指过盈啮合剃齿。
制动剃齿法
是指在剃齿过程中,采用制动加压法来制动被动的刀具或齿轮的轴,将必须的压力加于啮合齿面。这种剃齿法,对以下两种情况比较方便:只需要加工一侧齿面;剃具刀和齿轮以任意啮合角啮合进行剃齿。这种方法可以通过制动转矩的任意调节而连续地改变切削压力,所以大多用于大型齿轮齿形误差的矫正。
滚光剃齿法
用同时有剃齿作用和滚光作用的滚光剃齿刀对没有淬火的齿轮进行的剃齿加工,称为滚光剃齿法。这种加工法,既可以提高齿形精度,又可以降低齿面粗糙度。滚光剃齿可以在齿滚光机或一般铣床上采用特殊的夹具来进行。加工过程中刀具和工件的轴线是平行的。
滚光剃齿刀沿轮缘刻着槽,槽比齿高略深,加工斜齿轮用具有环形槽的斜齿滚光剃齿刀(其斜角应和被加工齿轮齿的斜角相同,但方向相反)(图11-8)。加工直齿轮应采用具有螺旋槽的直齿剃齿刀。这些环形槽或螺旋槽就是剃齿刀特殊的切削刃。
滚光剃齿与剃齿一样,剃齿刀对工件施加径向压力,在剃削的同时,进行着使齿面形成光滑而光亮的表面冷作(滚压)硬化。这种方法适用于高精度、低噪声、不经热处理的齿轮。
鼓形剃齿法
鼓形剃齿法是剃削鼓形齿轮的剃齿法。鼓形剃齿法一般采用两种方法:一种是用具有摇摆工作台机构的剃齿机加工(图11-9a)。当工作台绕中心摆时,在齿轮两端可以剃去较多金属。另一种是在剃齿刀磨刃时将齿向磨成逆鼓形(图11-9b)。这样,剃齿后的齿轮向具有鼓形,这种刀具也称为凹形剃齿刀。这一种方法为切向剃齿法和对角剃齿法所采用。
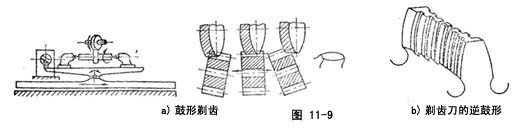
珩齿
珩齿是用来对热处理后的齿轮进行精加工的一种方法。它是利用珩轮在与被珩齿轮相啮合过程中,借助齿面间的压力和相对滑动来进行切齿的方法。在运动关系上珩齿和剃齿是相同的。
珩轮是含有磨料的塑料齿轮。珩磨速度远比磨削时低,珩磨切削过程的本质,是低速磨削、研磨和抛光的综合过程。珩轮弹性大,使珩齿修正误差的能力不如剃齿强,而其本身的误差也不会全部反映到齿轮上。因此对珩轮本身的精度勿需要求太高,而对珩前的齿轮则要求较高的精度。
珩齿可用于消除齿轮热处理后产生的误差,降低齿面粗糙度;去除齿面损伤、毛刺和降低齿轮副的噪声等。与磨齿、研齿等精加工方法相比,具有较高的生产率,一般可用于加工6~8级精度的齿轮。珩齿加工可分为定隙珩齿法、定压珩齿法和变压珩齿法。
珩齿加工中使用的珩轮,是由轮心和齿圈两部分组成的齿轮,如图11-10所示。轮心多采用钢料制造。齿圈材料的基本成分有磨料、树脂或金属粘结剂和固化剂等。珩轮的制造是使用专门的模具,把齿圈材料中各种成分的混合物浇注并粘结在轮心上制成的。
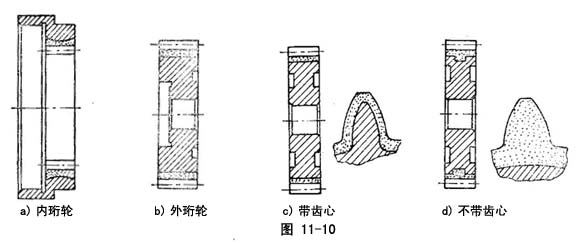
定隙珩齿法
在珩齿过程中,珩轮与齿轮工件之间保持着预定的啮合间隙(单面啮合)。工件具有可控制的制动力,使珩齿在一定的压力下进行。这种珩齿方式可降低齿面粗糙度,略微能修正热处理变形,但不能修正齿轮工件的偏心误差。
变压珩齿法
在珩齿过程中,珩轮与工件保持无隙啮合,并有一定压力。随着珩磨的进行,压力逐渐减小,直到接近消失,此法能显著地修正齿轮的几何偏心误差。但这种珩齿法在进行过程中,工件齿顶与珩轮齿面根部接触,珩轮齿面的磨损使其根部造成台阶,如图11-11所示。珩轮必须经过修磨才能继续使用,降低了珩轮的耐用度。
定压珩齿法(三点啮合珩齿法)
在整个珩齿过程中,珩轮与工件始终在预定的压力下保持无隙啮合,其压力由辅助机构控制。这种方法能有效地修正齿轮误差。
定压珩齿过程中,能消除工件齿顶圈和珩轮齿根圆间的径向间隙,同时轮齿啮合时齿廓两侧齿面都接触,形成了三点啮合,如图11-12所示。这种三点啮合的定压珩磨方式能使珩轮齿面及齿根连续磨损,磨损后形成新的齿面(再生齿面),可继续珩磨齿轮,提高珩轮寿命,其寿命比普通双面啮合珩齿法能提高3~4倍,是一种比较完善的珩齿法。
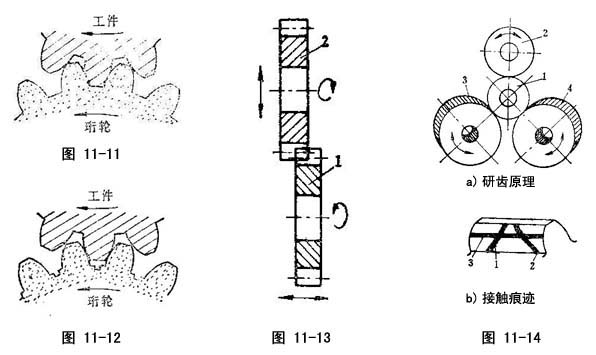
研齿
研齿是齿轮光整加工方法之一。其原理是用研磨轮(形状与齿轮相似,可为外齿轮或内齿轮)与被研齿轮在轻微制动下相互啮合,并在齿面间加入研磨剂,利用其相对滑动,在被研齿轮的齿面上研去一层极薄的金属,达到降低齿面粗糙度和校正齿轮部分误差的目的。
研磨钢齿轮时,通常选用细粒灰铸铁作研磨轮材料。研磨轮的直径应尽量选大一点,可增加重磨次数与提高耐用度。为了保证磨料混合液所需的侧隙,研轮的齿厚应当比被研齿轮齿厚小0.045~0.065mn。研齿的精度主要取决于研前齿轮的精度和研磨轮本身的精度,所以研磨轮的精度应比被研齿轮的精度高1级或相等。
研磨剂采用液体或稠的磨料混合物。研磨钢质淬火齿轮时选用230°~270°的刚玉或电刚玉(Al2O3)与机油、黄油的混合物,或者选用氧化铬和硬脂酸的混合物。
研齿过程中,为了防止被研齿轮齿形精度降低,研齿时间不宜过长。研磨余量一般在径向留0.01~0.04mm;研齿的切削速度通常选取0.5~1m/s或者再低一些,视被研齿轮热处理后的变形情况而定。
研齿一般应用于圆柱齿轮(直齿、斜齿和内齿)和圆锥齿轮热处理后的齿面光整加工。研齿方法分平行轴研齿法和交错轴研齿法两种。
平行轴研齿法
此法原理如图11-13所示。被加工齿轮1缓慢旋转,并沿其轴线方向作快速往复运动。研磨轮2由被加工齿轮带动旋转,并作短促的径向进给运动。经过一定的加工时间后,改变旋转方向,加工轮齿的另一面。和其他加工方法不同的是,在研齿机上没有径向载荷加到研磨轮上,而是用制动器在研轮上加制动转矩,以此达到增大齿面间压力,使磨料嵌入研轮齿面,加速研磨过程。
该方法优点是:机床结构简单,可用旧机床改装,也可采用简易研齿夹具在一般车床上进行研齿。
交错轴研齿法
研齿原理如图11-14所示。被加工齿轮1与研轮2、3、4相互啮合,并带动被制动着的研轮旋转,同时被加工齿轮作轴向往复运动。经过一定加工时间后,改变其旋转方向,再加工齿轮的另一面。交错轴研齿,研轮主轴的安装与工件轴线成一定的轴交角。通常仅二个研轮装成交错轴线,第三个研轮装成与工件轴线平行。研磨直齿轮时,研轮2应为直齿,其轴线与工件轴线平行;3和4应为螺旋齿,其轴线与工件轴线交错,相对滑动量大,加速了研磨作用;啮合点沿齿长逐渐移动,均匀地研掉齿面上的金属。因此研磨精度和生产率都优于平行轴研齿法。安装第三个与工件轴线平行的研轮的目的在于保证啮合齿成线接触(图11-14b),可以修正其余两个研轮没有研掉的部分。
该方法研齿机构复杂,不易用一般机床改装,所以尚未广泛应用。
齿条 |
圆柱齿轮 |
圆锥齿轮 |
蜗轮蜗杆 |
非圆齿轮 |
特种齿轮
首页 |
进口齿条 |
进口齿轮 |
齿轮标准 |
询价必读 |
齿轮知识 |
网站地图 电话:010-6492-5308 | 传真:010-6492-5744 | 邮件:
sales@gearandrack.cn
2003-2012年北京正基元齿轮有限公司版权所有。本网站由北京正基元齿轮有限公司设计、制作、维护。
本网站上的任何内容,未经正基元公司的书面授权,均不得以任何方式复制、转载、或镜像,否则将追究其违权责任。 |